Hochleistungspolymere (Teil 2): ein genauer Blick auf PEEK
Was ist PEEK?
PEEK oder Polyetheretherketon gehört zu einer Familie von Polymeren, die als aromatische Polyketone (oder genauer „Polyaryletherketone“ oder PAEK) bezeichnet werden. Das heißt, es ist aus den folgenden Bausteinen aufgebaut:
Die Forschung und Entwicklung zu PAEK begann in den 1960er-Jahren, aber erst 1978 wurde von dem britischen Chemieunternehmen ICI (Imperial Chemical Industries) ein Patent auf PEEK angemeldet und 1981 erstmals VICTREX PEEK-Polymer auf den Markt gebracht.
„Aromatisch“ bedeutet im allgemeinen Sprachgebrach würzig, wohlschmeckend oder -riechend; in der Wissenschaft beschreibt es Moleküle, die ringförmige Strukturen (wie der Aryl-Baustein oben) aufweisen oder daraus bestehen. Kleine Moleküle dieser Art wie Toluol und Naphthalin besitzen einen ausgeprägten Geruch – daher der Name. PEEK ist jedoch, wie die meisten Thermoplaste, unter normalen Bedingungen geruchlos. Chemisch gesehen ist PEEK ein vorwiegend lineares, teilkristallines Polymer. Seine Bausteine verknüpfen sich wie folgt zu Ether-Ether-Keton (EEK):
Die in den eckigen Klammern dargestellte Repetiereinheit wird im Durchschnitt zwischen 200 und 300 Mal repliziert, um eine einzige PEEK-Polymerkette zu bilden. Das P steht für griechisch „Poly“, was „viele“ bedeutet. Aus vielen EEKs wird PEEK. Die Aryl- und Ketongruppen sind ziemlich starr und ergeben eine Steifigkeit, die zu guter mechanischer Leistungsfähigkeit in Verbindung mit hohem Schmelzpunkt führt. Die Ethergruppen sorgen für ein gewisses Maß an Flexibilität in puncto Zähigkeit. Sie sind wie die Aryl- und Ketongruppen nicht reaktionsfreudig, woraus sich chemische Beständigkeit ableiten lässt. Aufgrund der regelmäßigen Struktur der Repetiereinheit können PEEK-Moleküle teilweise kristallisieren. Die Kristallinität führt zu einer Kombination aus Verschleiß-, Kriech-, Ermüdungs- und chemischer Beständigkeit dazu später mehr.
Das daraus resultierende Polymer gilt weithin als einer der leistungsfähigsten Thermoplaste. Im Unterschied zu Metallen haben PEEK-basierte Materialien sehr geringes Gewicht, sind leicht zu formen, korrosionsbeständig und können eine wesentlich höhere spezifische Festigkeit (Festigkeit pro Gewichtseinheit) aufweisen.
Auf die Anwendung angepasstes Produkt
Bei der Herstellung von PEEK verwenden wir ein Verfahren, das die Länge der Ketten bzw. das Molekulargewicht kontrolliert. PEEK mit längeren Ketten (hohes Molekulargewicht oder „MW“) ist in der Regel zäher und schlagfester als PEEK mit kurzen Ketten. Polymere mit hohem MW sind jedoch im geschmolzenen Zustand sehr zähflüssig, und können daher nur schwer in kleine Formwerkzeuge gefüllt werden. PEEK mit niedrigem MW ist weniger schlagfest, fließt jedoch in der Schmelze viel besser, sodass sich damit problemlos kleine, filigrane Teile herstellen lassen.
Eine Reihe attraktiver Eigenschaften
PEEK bietet nicht nur zwei oder drei Eigenschaften, die es als Polymer der Wahl auszeichnen, wenn hohe Leistung erforderlich ist; es besitzt eine ganze Reihe davon:
-
Hohe Hitzebeständigkeit:
Tests haben gezeigt, dass VICTREX PEEK-Polymer eine Dauergebrauchstemperatur von 260° C (500° F) hat. Dadurch kann es sich für eine Bandbreite von Anwendungen in thermisch anspruchsvollen Umgebungen eignen, wie sie z. B. in der Verfahrenstechnik, im Öl- und Gassektor sowie in Motoren und Getrieben von Millionen von Fahrzeugen zu finden sind. PEEK kann den Gleit-Reib-Bedingungen in dynamischen Anwendungen wie Anlaufscheiben und Dichtungsringen widerstehen.
-
Hohe Chemikalienbeständigkeit:
PEEK kann in chemisch aggressiven Betriebsumgebungen, z. B. in Bohrlöchern der Öl- und Gasindustrie, oder in Getrieben von Maschinen- und Fahrzeugen eingesetzt werden, ohne durch die Chemikalien Schaden zu nehmen. Der Hochleistungsthermoplast kann auch Kerosin, Hydraulikflüssigkeiten, Enteisungsmitteln und Insektiziden, die in der Luftfahrtindustrie verwendet werden, widerstehen. Das gilt für weite Bereiche von Druck und Temperatur über lange Zeiträume.
-
Mechanisch fest:
PEEK zeigt über einen weiten Temperaturbereich hervorragende Festigkeit und Steifigkeit. Kohlefaserverbundwerkstoffe auf PEEK-Basis besitzen ein Vielfaches der spezifischen Festigkeit von Metallen und Legierungen. Unter „Kriechen“ versteht man bei einem Material, das es bei konstanter Beanspruchung über einen längeren Zeitraum dauerhaft verformt wird. Mit „Ermüdung“ wird das spröde Versagen eines Materials unter wiederholter zyklischer Belastung bezeichnet. PEEK besitzt dank seiner teilkristallinen Struktur sowohl eine hohe Kriech- als auch Ermüdungsbeständigkeit. Es hat sich gezeigt, dass es über eine lange Einsatzdauer hinweg langlebiger ist als viele andere Polymere und einige Metalle.
-
Schwer entflammbar:
PEEK besitzt hervorragende Eigenschaften, die mit einem Brand in Verbindung zu bringen sind. Es widersteht einer Verbrennung bis fast 600° C (schwer entflammbar). Wenn es bei sehr hohen Temperaturen zum Brennen gebracht werden kann, wird die Verbrennung nicht unterstützt (schwer brennbar) und es entsteht nur wenig Rauch (geringe Rauchgasdichte). Dies ist ein Grund, warum PEEK in Verkehrsflugzeugen häufig verwendet wird.
-
Wiederverwertbar und recycelbar:
Das PEEK-Molekül ist sehr stabil, sodass das Polymer bei minimalen Änderungen seiner Eigenschaften immer wieder aufgeschmolzen und erneut verarbeitet werden kann. Dies trägt zur Ökobilanz bei und kann sicherstellen, dass Abfälle aus Fertigungsprozessen wirtschaftlich wiederverwendet werden können.
- PEEK kann noch viel mehr!
PEEK nimmt auch keine Feuchtigkeit auf und ändert daher seine Eigenschaften in feuchter Umgebung nicht. Es widersteht Gamma- und Elektronenstrahlen und ist für Röntgenstrahlen durchlässig, was es für medizintechnische Anwendungen interessant macht. Auch die elektrischen Eigenschaften sind beachtenswert: PEEK wird häufig als elektrischer Isolator verwendet, lässt sich jedoch auch modifizieren, um elektrisch leitend zu sein oder elektrostatisch abzuleiten.
Als thermoplastischer Kunststoff kann PEEK mit herkömmlichen thermoplastischen Verarbeitungsmaschinen für Spritzgießen und Formpressen sowie für Extrusion verarbeitet werden. Es ist sehr vielseitig und wird zunehmend für verbesserte Langlebigkeit, Gewichtsersparnis und insgesamt zur Reduktion der Lebenszykluskosten von Bauteilen verwendet. Kein Wunder, dass es Metalle und Legierungen ersetzt!
In vielen Industrien und kritischen Umgebungen stehen Materialexperten, Konstrukteure und Einkäufer vor der Entscheidung, ob sie an herkömmlichen Metalle und Legierungen festhalten oder ob PEEK das Material der Wahl ist, um Fortschritte in Bezug auf Leistung, Gewichtsreduzierung, Energieverbrauch, Montagezeit und Kosten zu erzielen.
Über den Autor
John Grasmeder, Chief Scientist bei Victrex
Dr. John Grasmeder verfügt über mehr als 25 Jahre Erfahrung in der Kunststoffindustrie, in Forschung und Entwicklung, kaufmännischen und führenden Positionen bei ICI, BASF, Hoechst und Shell Joint Ventures in Großbritannien und in Deutschland. Er ist seit 11 Jahren bei Victrex, war ab 2010 der technische Direktor und ist seit 2016 „Chief Scientist“.
Über den Autor/die Autorin
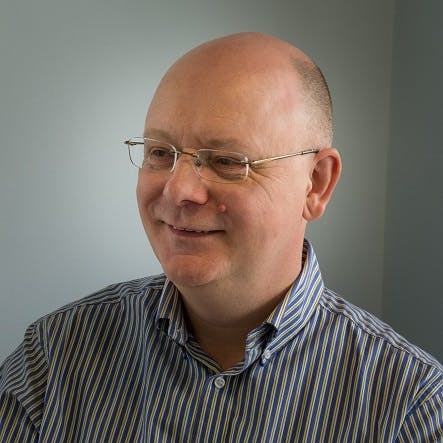
Entdecken Sie den Victrex Blog
Alle Blogartikel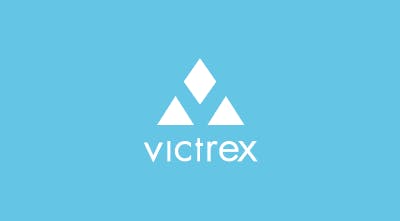
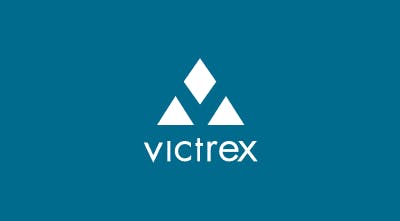
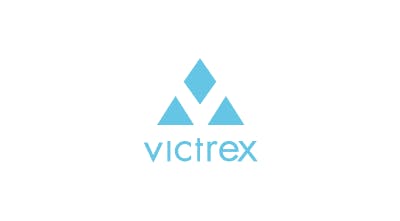
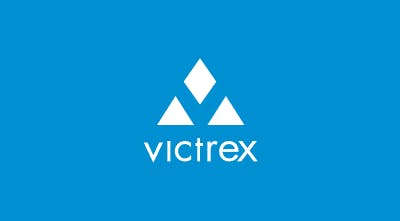