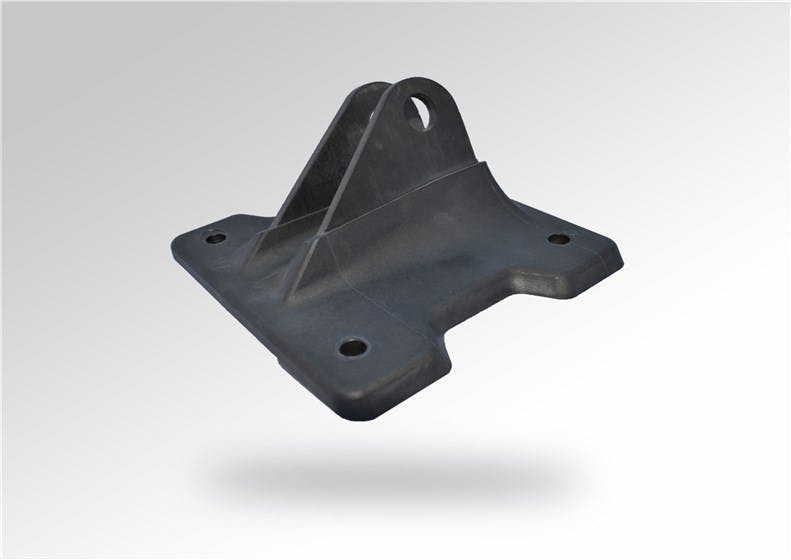
Safran Cabin, ein weltweit führender Anbieter von Kabineninneneinrichtung, und Victrex haben gemeinsam eine flexible Plattform für die Qualifizierung von Bauteilen aus thermoplastischen Verbundwerkstoffen im Flugzeugbau entwickelt. Ziel ist es, so die Planung und Markteinführung verschiedener Halterungen (Brackets) zu verkürzen. Die erste Halterung soll in der Flugzeugkabine eingesetzt werden; sie besteht aus dem PAEK*-Kohlefaserverbundwerkstoff VICTREX AE™ 250, der mit VICTREX™ PEEK-Polymer umspritzt wird. Als ein weltweit führender Anbieter von Lösungen aus Hochleistungspolymeren stellt Victrex das erforderliche Know-how in Bezug auf Material, Fertigung und Werkzeuge zur Verfügung, damit vielfältige Konstruktionsmerkmale realisiert und gleichzeitig wesentliche Leistungsparameter erfüllt werden können. Safran Cabin bringt entscheidendes Fachwissen bei Konstruktion und Fertigung ein, um die Anwendbarkeit in Service- und Zertifizierungsprozessen im Flugzeugbau sicherzustellen.
„Wir müssen auf die vielen Anforderungen bei Flugzeughalterungen und ähnlichen Strukturbauteilen Antworten finden, wobei jeder Fall eine Reihe von Fragen in puncto Beanspruchung, Einschränkungen und Belastung mit sich bringt“, sagte Tyler Smithson, Senior R&T Engineer bei Safran Cabin. „Der Schlüssel zum Erfolg liegt in der Entwicklung einer flexiblen Composite-Plattform, die für mehrere Projekte eingesetzt werden kann. Sie reduziert unsere Teilezahl und die Designkomplexität, verkürzt die Markteinführungszeit und beschleunigt die Umsatzrendite. In Zusammenarbeit mit Victrex sind wir der Meinung, dass wir das erreicht haben!“
Die beiden Unternehmen verwendeten eine innovative Technik, bei der VICTREX AE™ 250-Composite mit VICTREX™ PEEK-Hochleistungspolymer umspritzt wird. Dieser „Hybrid Moulding“-Verarbeitungsansatz von Victrex ist eine skalierbare und standardisierte Technologie. Sie hat das Potenzial, Kunden im kommerziellen Flugzeugbau dabei zu unterstützen, Herausforderungen wie notwendige niedrigere Ausschussraten, schnellere Zykluszeiten, Teilekonsolidierung und Reduzierung der sekundären Fertigungsschritte zu meistern. Strenge Testverfahren und Qualifizierungen weisen darauf hin, dass entsprechende Strukturbauteile für Flugzeuge hohen mechanischen Belastungen standhalten können.
Flugzeugkonstruktion der Zukunft vorantreiben
Während des Entwicklungsprozesses hat sich Safran Cabin darauf konzentriert, Teile und Formwerkzeuge zu bestimmen, die für verschiedene Halterungen adaptiert werden können. Ziel ist es, modulare Baureihen zu erhalten, die mit dem gleichen Formwerkzeug kompatibel sind. So lassen sich Kostenvorteile erschließen und aufgrund der eingesetzten Materialien auch Gewichtseinsparungen erreichen.
In der ersten konzeptionellen Konstruktionsphase wurden Formfüllungs- und Struktursimulationsmethoden mit verschiedenen physikalischen Testtechniken kombiniert, um eventuelle Fehlermöglichkeiten bei der neuen Technologie zu identifizieren und zu beheben sowie Spritzgussfertigung und Kosten zu optimieren. Kritische Merkmale wurden definiert und ein wirtschaftlicher, standardisierbarer Konstruktionsprozess entwickelt.
„Victrex gelingt es immer wieder erfolgreich, ‚disruptive‘ Technologieansätze in den von uns bedienten Industriezweigen einzuführen, indem wir unser Verarbeitungs- und Polymer-Know-how einsetzen, um den Vermarktungsprozess zu beschleunigen“, kommentiert Tim Herr, Director Aerospace bei Victrex. „Hybrid Moulding, auch Hybridspritzguss genannt, und VICTREX AE 250-Verbundwerkstoffe zählen sicher zu dieser Kategorie, aber das ist erst der Anfang. Wir werden unser Portfolio weiterhin mit der Unterstützung unserer Kunden und Partner testen, um das volle Potenzial dieser Werkstoffe aufzuzeigen.“
Überlegene Leistung: Halterungen sollen in diesem Jahr in Produktion gehen
Die ersten Prototypen wurden bereits bei Tri-Mack Plastics Manufacturing Corporation hergestellt. Im Vergleich zum ursprünglichen Aluminiumbauteil konnten diese bis zu 20 Prozent Kosteneinsparungen, 50 Prozent Gewichtsersparnis und ein etwa fünffach besseres Buy-to-Fly-Verhältnis erzielen. Derzeit ist die Halterung für die Endprüfung und Qualifizierung von Produktionsteilen vorgesehen. Es ist geplant, dass die Composite-Brackets im Laufe des Jahres 2019 in Produktion gehen.
Tech-Paper-Präsentation auf der CAMX
Titel: „Developing a Hybrid PAEK Overmoulded Thermoplastic Composite Bracket“
Zeit: Dienstag, 24. September 2019, 14:3014:55 Uhr, Anaheim Convention Center I 210D.
Veranstaltungsort: CAMX, the composites and advanced materials expo; 23. bis 26. September 2019, Anaheim, Kalifornien/USA.
Victrex auf der K 2019 in Düsseldorf: Meet-the-Expert
Thermoplastische Composite-Lösungen für die Luftfahrtindustrie stellen einen der Schwerpunkte am Stand von Victrex auf der K 2019 dar. Zu dem Thema findet auch eine „Meet the expert“-Veranstaltung in englischer Sprache statt: “The ascendance of thermoplastic composites” mit James Myers, Head of R&D - Aerospace & Composite Applications bei Victrex, direkt am Victrex-Stand am Donnerstag, 17. Oktober 2019, 17:30 Uhr, Halle 5 Stand B09.
*) Polyaryletherketon (PAEK) ist eine Gruppe von Hochleistungsthermoplasten wie Polyetheretherketonen (PEEK).
Über Safran Cabin
Safran Cabin ist der weltweit führende Anbieter von Kabineneinrichtung für Kurz-, Mittel- und Langstreckenflugzeuge in der kommerziellen und militärischen Luftfahrt. Die Produktpalette des Unternehmens umfasst integrierte Kabineninterieurs, Gepäckfächer, Küchen, Toiletten, Crewunterkünfte und Frachtcontainer.
„Wir müssen auf die vielen Anforderungen bei Flugzeughalterungen und ähnlichen Strukturbauteilen Antworten finden, wobei jeder Fall eine Reihe von Fragen in puncto Beanspruchung, Einschränkungen und Belastung mit sich bringt“, sagte Tyler Smithson, Senior R&T Engineer bei Safran Cabin. „Der Schlüssel zum Erfolg liegt in der Entwicklung einer flexiblen Composite-Plattform, die für mehrere Projekte eingesetzt werden kann. Sie reduziert unsere Teilezahl und die Designkomplexität, verkürzt die Markteinführungszeit und beschleunigt die Umsatzrendite. In Zusammenarbeit mit Victrex sind wir der Meinung, dass wir das erreicht haben!“
Die beiden Unternehmen verwendeten eine innovative Technik, bei der VICTREX AE™ 250-Composite mit VICTREX™ PEEK-Hochleistungspolymer umspritzt wird. Dieser „Hybrid Moulding“-Verarbeitungsansatz von Victrex ist eine skalierbare und standardisierte Technologie. Sie hat das Potenzial, Kunden im kommerziellen Flugzeugbau dabei zu unterstützen, Herausforderungen wie notwendige niedrigere Ausschussraten, schnellere Zykluszeiten, Teilekonsolidierung und Reduzierung der sekundären Fertigungsschritte zu meistern. Strenge Testverfahren und Qualifizierungen weisen darauf hin, dass entsprechende Strukturbauteile für Flugzeuge hohen mechanischen Belastungen standhalten können.
Flugzeugkonstruktion der Zukunft vorantreiben
Während des Entwicklungsprozesses hat sich Safran Cabin darauf konzentriert, Teile und Formwerkzeuge zu bestimmen, die für verschiedene Halterungen adaptiert werden können. Ziel ist es, modulare Baureihen zu erhalten, die mit dem gleichen Formwerkzeug kompatibel sind. So lassen sich Kostenvorteile erschließen und aufgrund der eingesetzten Materialien auch Gewichtseinsparungen erreichen.
In der ersten konzeptionellen Konstruktionsphase wurden Formfüllungs- und Struktursimulationsmethoden mit verschiedenen physikalischen Testtechniken kombiniert, um eventuelle Fehlermöglichkeiten bei der neuen Technologie zu identifizieren und zu beheben sowie Spritzgussfertigung und Kosten zu optimieren. Kritische Merkmale wurden definiert und ein wirtschaftlicher, standardisierbarer Konstruktionsprozess entwickelt.
„Victrex gelingt es immer wieder erfolgreich, ‚disruptive‘ Technologieansätze in den von uns bedienten Industriezweigen einzuführen, indem wir unser Verarbeitungs- und Polymer-Know-how einsetzen, um den Vermarktungsprozess zu beschleunigen“, kommentiert Tim Herr, Director Aerospace bei Victrex. „Hybrid Moulding, auch Hybridspritzguss genannt, und VICTREX AE 250-Verbundwerkstoffe zählen sicher zu dieser Kategorie, aber das ist erst der Anfang. Wir werden unser Portfolio weiterhin mit der Unterstützung unserer Kunden und Partner testen, um das volle Potenzial dieser Werkstoffe aufzuzeigen.“
Überlegene Leistung: Halterungen sollen in diesem Jahr in Produktion gehen
Die ersten Prototypen wurden bereits bei Tri-Mack Plastics Manufacturing Corporation hergestellt. Im Vergleich zum ursprünglichen Aluminiumbauteil konnten diese bis zu 20 Prozent Kosteneinsparungen, 50 Prozent Gewichtsersparnis und ein etwa fünffach besseres Buy-to-Fly-Verhältnis erzielen. Derzeit ist die Halterung für die Endprüfung und Qualifizierung von Produktionsteilen vorgesehen. Es ist geplant, dass die Composite-Brackets im Laufe des Jahres 2019 in Produktion gehen.
Tech-Paper-Präsentation auf der CAMX
Titel: „Developing a Hybrid PAEK Overmoulded Thermoplastic Composite Bracket“
Zeit: Dienstag, 24. September 2019, 14:3014:55 Uhr, Anaheim Convention Center I 210D.
Veranstaltungsort: CAMX, the composites and advanced materials expo; 23. bis 26. September 2019, Anaheim, Kalifornien/USA.
Victrex auf der K 2019 in Düsseldorf: Meet-the-Expert
Thermoplastische Composite-Lösungen für die Luftfahrtindustrie stellen einen der Schwerpunkte am Stand von Victrex auf der K 2019 dar. Zu dem Thema findet auch eine „Meet the expert“-Veranstaltung in englischer Sprache statt: “The ascendance of thermoplastic composites” mit James Myers, Head of R&D - Aerospace & Composite Applications bei Victrex, direkt am Victrex-Stand am Donnerstag, 17. Oktober 2019, 17:30 Uhr, Halle 5 Stand B09.
*) Polyaryletherketon (PAEK) ist eine Gruppe von Hochleistungsthermoplasten wie Polyetheretherketonen (PEEK).
Über Safran Cabin
Safran Cabin ist der weltweit führende Anbieter von Kabineneinrichtung für Kurz-, Mittel- und Langstreckenflugzeuge in der kommerziellen und militärischen Luftfahrt. Die Produktpalette des Unternehmens umfasst integrierte Kabineninterieurs, Gepäckfächer, Küchen, Toiletten, Crewunterkünfte und Frachtcontainer.