Lighter, Faster, Greener: The Pursuit for the Shape of Aerospace’s Future
Transitioning to carbon neutrality
The aviation industry today generates almost 3% of all global CO2. By 2050, it’s predicted that demand for flights will have increased three-fold. If this doesn’t change, emissions from aircrafts will double between now and then, bringing them to upwards of 300% over and above 2005 levels1.
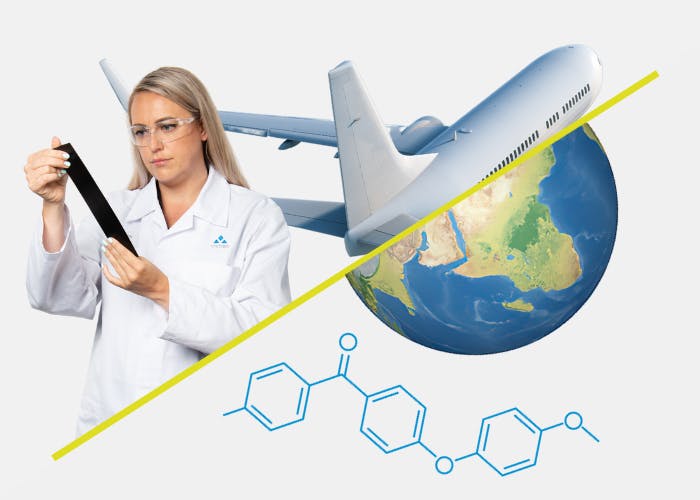
Because of this, in October 2022, following the lead of many other industries, member states of the International Civil Aviation Organization (ICAO) agreed to aim to achieve net-zero carbon dioxide emissions by 20502. Meanwhile, at the International Air Transport Association’s (IATA) 77th Annual General Meeting, a resolution was approved stating that the global air transport industry should aim for net-zero carbon emissions by 20503. Both commitments align with the Paris Agreement’s goal for global warming, which is of course trying to limit the Earth’s warming to 1.5°C. This is a challenging target, considering that it typically takes about 10+ years to develop a new aircraft.
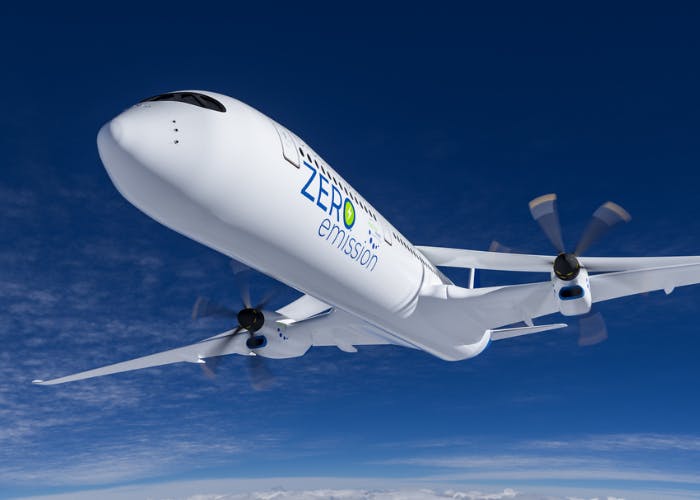
The composite materials flying today
The use of game-changing technology to improve energy use and reduce net greenhouse gas emissions will be at the heart of these tasks. As such, focus needs to be placed on designing and developing the next generation of aircrafts – ones that are radically more efficient than those that are currently in use.
In a bid to work towards this, initiatives have been launched - with major airframers, tiers, material suppliers, and institutes joining forces – both worldwide and by regions – (e.g. Clean Aviation, Hi-Rate Composites Aircraft Manufacturing (HiCAM) Project) funding research programmes that seek to examine existing and new technologies while demonstrating their various benefits.
The timeless principle in making planes more efficient, is to make them lighter. Composites have been the pioneering material - with their winning combination of high strength, low weight and durability – they are being referred to as the shape of aerospace’s future4.
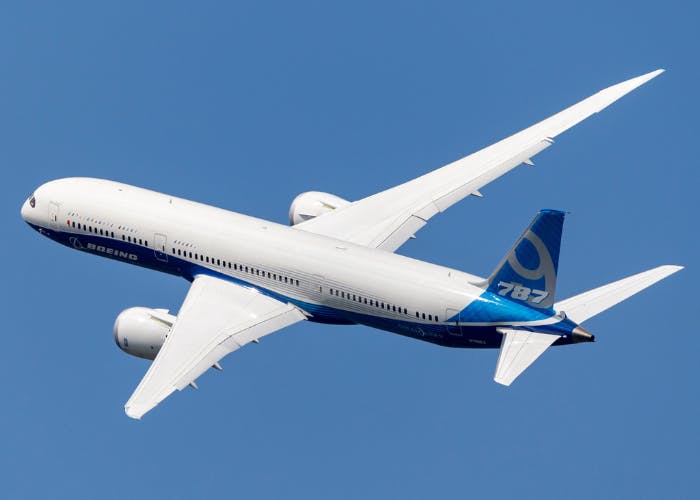
The flagship long-haul aircrafts by major airframers already utilise 50% composite materials in their construction by weight, and 80% by volume.5 A study published in the International Journal of Life Cycle Assessment estimates that by 2050, composite planes could reduce emissions from a global fleet by 14-15% – compared to a fleet that maintains its existing aluminium-based configuration.6
Change needed
However, composite materials in these planes also have their challenges. They are based on thermosets – that can’t be recycled and have short shelf-lives.7 The machining process carry the risk of health impacts for operators8, incur long production lead times and can’t be welded, which leads to aircraft assembly inefficiencies.
The aviation industry initiatives are now working hard to leverage the art of manufacturing lightweight planes – making them faster and greener – to reduce the plane’s economic and environmental impact from manufacturing.
LMPAEK™ Polymer - the breakthrough material
The invention of LMPAEK™ polymer by Victrex, is rapidly gaining presence as a breakthrough in addressing many of these challenges.
Victrex has a long history within the aerospace industry and strong relationships with the major airframers. The journey of developing and becoming the sole manufacturer of LMPAEK™ polymer began from a need for change within the industry – to address the challenges of scalability, cost, performance and processability of existing materials.
The primary motivation for creating LMPAEK™ polymer was to make processing easier at much lower temperatures but keeping its high temperature properties.
The other feature of this new polymer is its slower speed of crystallisation. PEEK crystallises extremely quickly which is beneficial in injection moulding applications, whereas in composites processing, becomes suitable to crystallise more slowly as this helps lay-up and consolidation, especially out-of-autoclave [Fig 1]. This feature also gives the potential for welding large structural parts during assembly. [Fig 2]
Fig 1: Layup comparison of PEEK and LMPAEK
The forefront of material science
LMPAEK™ materials are already available in multiple forms – including tape, film, filament, compound and powder – and because of how it is processed, parts can be made faster, cheaper and greener.
By working alongside Daher, together we have shown that VICTREX AE 250 LMPAEK™ UDT enables the manufacturing of much thicker and high-quality composite laminates. To date, these are up to 176 layers thick, compared to the norm of 32.
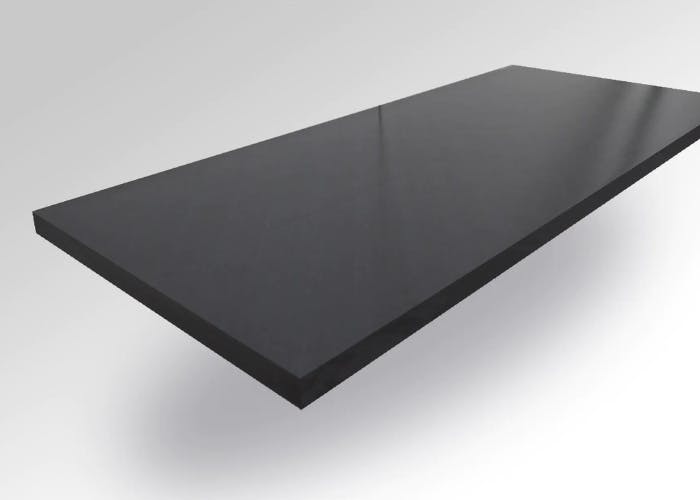
A recent demonstration from Qarbon Aerospace at the Paris Airshow 2023 highlighted that welding a structural part made with LMPAEK™ material is approximately 40X faster than riveting the same part made with a thermoset composite.
What we are starting to see, is mounting evidence that this approach is working well, with very positive reactions from the market. At the most recent International Conference and Exhibition on Thermoplastic Composite (ITHEC), 75% of the technical papers presented mentioned LMPAEK™ polymer or parts.
Let’s make change
At Victrex we use our 40+ years’ experience of working with pioneering manufacturers, to identify and calculate the potential benefits and value of replacing existing materials and parts with polymer alternatives – helping OEMs from various industries identify the technologies and solutions that they need to adopt in order to realise their vision.
Working together, we have the vision, the tools and the products to support the changes to lighter, cheaper, faster and greener material alternatives, making the aero industry a much more sustainable one.
Let’s make change.
References
- https://www.weforum.org/agenda/2022/12/aviation-net-zero-emissions/
- https://www.iata.org/en/pressroom/2022-releases/2022-10-07-01/
- https://www.iata.org/en/programs/environment/flynetzero/
- https://www.airbus.com/en/newsroom/news/2017-08-composites-airbus-continues-to-shape-the-future
- Advanced materials emerge as challenging new frontier for aircraft recycling | In depth | Flight Global
- https://www.cam.ac.uk/research/news/lighter-planes-are-the-future
- Thermosets: How to Avoid Incomplete Curing | American Laboratory
- Health risks from exposure to metal-working fluids in machining and grinding operations - PubMed (nih.gov)
About the authors
Gilles Larroque joined Victrex in 2011, he is in charge of the Strategic Marketing activity for the Aerospace Business Unit. Prior to joining Victrex, from 2005 to 2011, Gilles worked in the medical devices industry, for Zimmer Spine, in product development for spinal applications. He started his career in 2001 as a R&D mechanical engineer consultant in various positions in aerospace and defence sectors. Gilles graduated with an engineer degree in mechanical system from the University of Technology or Troyes (France) in 2001. Starting in 1999, he graduated also with a Master of Science Thesis in engineering from Florida Atlantic University (USA) in 2001.
Ryan Herrmann joined Victrex in 2022 and is the Marketing Communications Manager for Aerospace and Additive Manufacturing. Ryan has 19 years’ experience in the manufacturing industry holding positions in Technical Service, Quality Assurance, and Inside Sales before transitioning into Marketing Communications. Ryan graduated from Gwynedd Mercy University in 2006 with a Bachelor of Science in Business Administration and a concentration in Marketing.
About the author
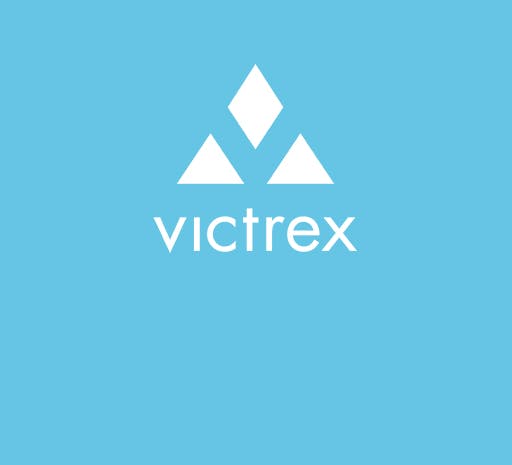