LMPAEK™ Explained and why it’s suited to composites and additive manufacturing.
In my recent blog, "PEEK or PAEK, what’s in a name?" we covered the PAEK family and some of its members, finishing with the recent LMPAEK™ additions, VICTREX AE™ 250 UD tape and VICTREX AM™ 200 filament, which are based on co-polymers containing two rather than one repeat unit.
Let’s think about co-polymers in general, as they are present in many other polymer families as well. A linear polymer, consisting of a single repeat unit, A, forms polymer chains, a backbone, structured like this:
-A-A-A-A-A-A-A-A-A-A-A-A-A-A-A-
However, with a co-polymer, consisting of two repeat units, A and B, there are various possibilities. If there are equal quantities of A & B, there could be a regular alternating structure:
-A-B-A-B-A-B-A-B-A-B-A-B-A-B-A-B-
In fact, these structures are rare. More often, there is a statistical or random nature to how the repeat units combine, for this can be the nature of polymer chemistry! If there were 75% A and 25% B repeat units, one could envisage a backbone like this:
-A-A-B-A-B-A-B-B-A-A-A-B-A-A-A-A-A-B-A-A-
But there is another possibility, a so-called block co-polymer, where the repeat units appear, you guessed it, in blocks. Taking the 70:30 ratio of A and B again, this might look like this:
-A-A-A-A-B-B-B-B-B-B-A-A-A-A-A-A-A-A-A-A-
How the repeat units in backbone are arranged can influence how quickly the polymer crystallises, and the amount of crystallinity too. The polymer might crystallise in discrete regions of A and B, or in a disordered manner, or somewhere in between. This will have a decisive influence on the macroscopic properties of the polymer – its mechanical properties such stiffness and toughness, its resistance to fracture and even its chemical resistance.
The primary motivation for creating these PAEK co-polymers was to be able to process them at much lower temperatures by reducing the melting point, Tm, whilst still retaining the glass transition temperature, Tg, and hence keeping the high temperature properties. However, we were also able to improve the suitability of these polymers to the processes in which they are being deployed. Looking at each in turn:
VICTREX AE™ 250 UDT Designed for composites
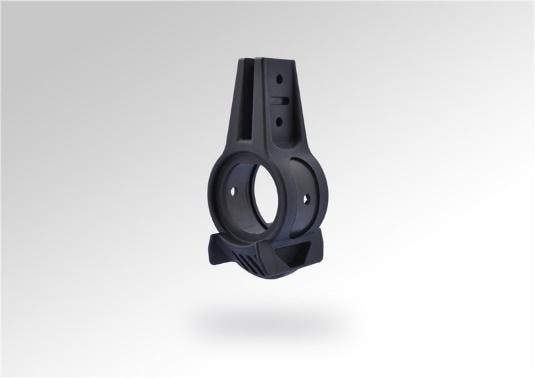
When we set out, we had a target to make the new polymer more suitable for composites processing than PEEK. Part of this was the lower processing temperature but we also targeted the speed of crystallisation. PEEK crystallises extremely quickly which can be beneficial in injection moulding applications, whereas in composites processing, we wanted a material which would crystallise more slowly as this aids lay-up and consolidation, especially out-of-autoclave.
High quality composite laminates
There is mounting evidence that this approach is working well. By working alongside Daher, we have together shown that VICTREX AE™ 250 UDT enables much thicker high-quality composite laminates to be manufactured, to date, up to 176 plies thick, compared to 32 as the norm.
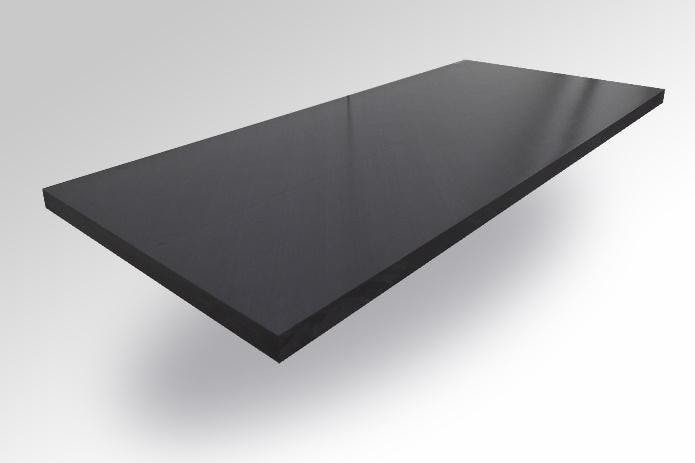
Thermoplastic composites match thermoset layup speed
More recently, working with Electroimpact, the goal of matching the layup speeds of thermosets has been achieved. The lower Tm also makes VICTREX AE™ 250 UDT ideal for overmoulding with compounds such as VICTREX PEEK 150CA30: the PEEK and the copolymer are fully miscible in the melt allowing the surface of the composite panel to fuse with the overmoulded compound resulting in good interfacial adhesion.
Ready to unlock the potential of LMPAEK™ for your applications?
With 40°C lower processing temperatures and enhanced manufacturing capabilities, LMPAEK™ polymers are transforming composites and additive manufacturing. Discover how these breakthrough materials can revolutionize your production processes.
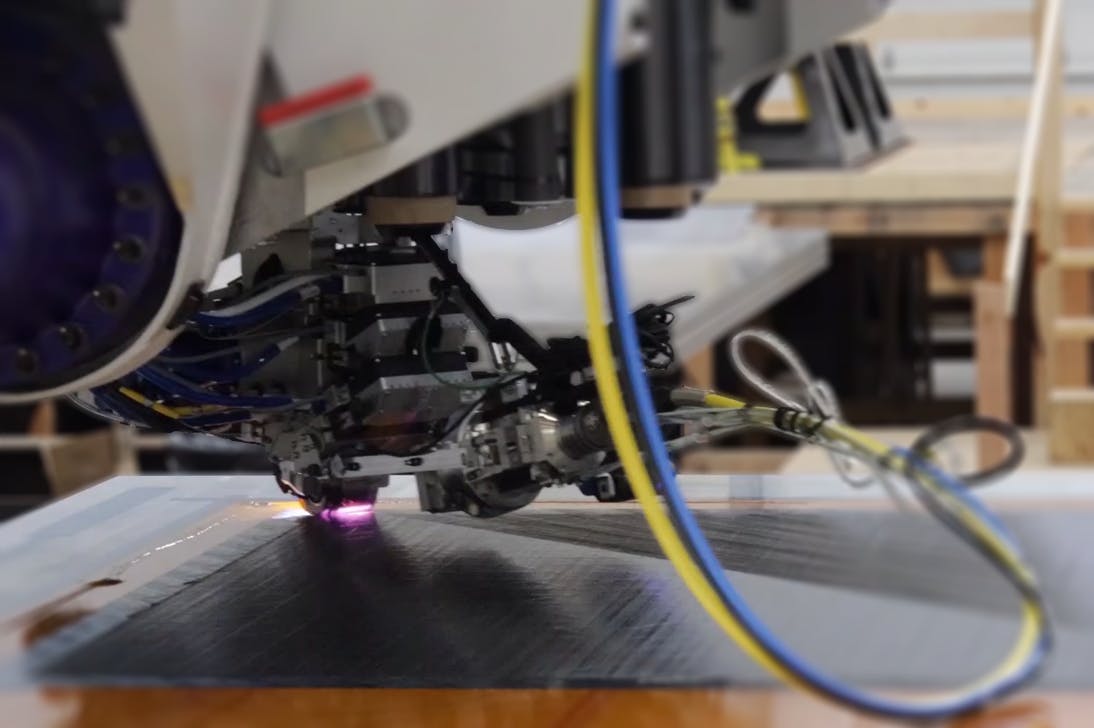
VICTREX AM™ 200 filament for Additive Manufacturing / 3D Printing
Historic challenges printing PAEK polymersUntil we developed VICTREX AM™ 200 filament, it was generally accepted that 3D-printing parts from semi-crystalline PAEKs was challenging: the poor adhesion between each layer. This is because once a layer is printed, there is generally a time lag until the next layer is printed on top of it, and the lower layer will have crystallised and cooled.
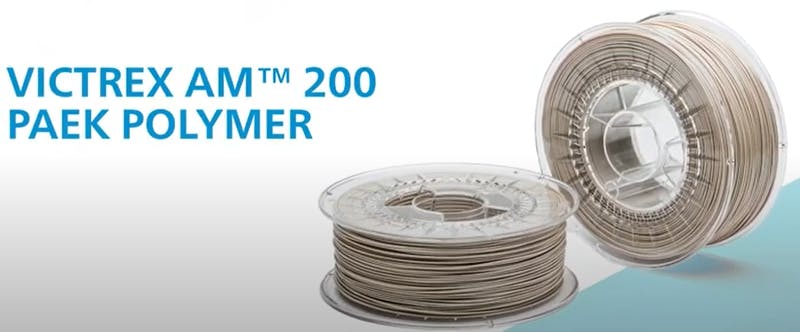
This led to poorer properties in the vertical Z-direction than in the X-Y plane, with the Z-direction sometimes being only 13-25% as strong as the X-Y. Although emerging technologies, such as Bond 3D, are addressing this.
VICTREX AM 200 permits a reduced processing temperature and has a dramatically slower crystallisation speed, so the Z-direction strength of parts can be up to 80% as strong as the X-Y plane and show more than 3 times the ductility of some grades of PEEK.
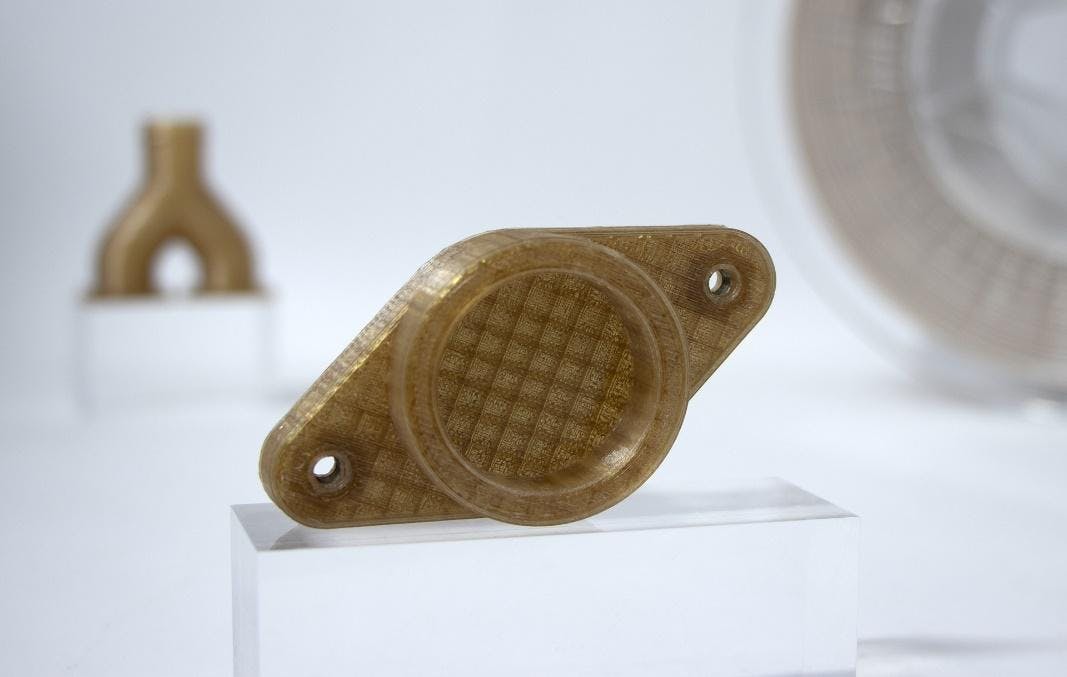
VICTREX AM™ 200 Designed and optimised for Additive Manufacturing.
Our partners at the University of Exeter’s Centre for Additive Layer Manufacturing (CALM) along with my colleagues have studied the reasons for this in detail and provided us with a deep understanding of why this works so well.
Summary
I hope that’s helped clarify some of the benefits of PAEK co-polymers. Whilst PEEK will continue to feature for many years to come, these new co-polymers will help solve different engineering challenges and PAEK-based advanced materials solutions will become more widely used than ever before in exciting new applications in the future.
© Victrex plc. 2021. All rights reserved.
Disclaimer
About the author
John Grasmeder, Chief scientist at Victrex
Dr John Grasmeder has over 25 years’ experience in the polymer industry, in R&D, commercial and business leadership positions at ICI, BASF, Hoechst and Shell joint ventures in both the UK and Germany. He has been with Victrex since 2005 and was Technical Director from 2010. He became Chief Scientist in 2016.
About the author
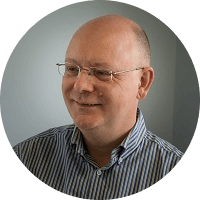