Five factors to consider when moulding PEEK
Polyetheretherketone (PEEK) is an advanced high-performance thermoplastic that is widely used in demanding applications in the aerospace, automotive, energy, industrial, electronics and medical industries.
One of the benefits of this semi-crystalline plastic is that it offers exceptional mechanical properties, temperature performance, and chemical resistance.
Even though injection moulding PEEK may be seen as challenging, it can be moulded similarly to other high performance thermoplastics and by focusing on some of PEEK’s unique processing requirements, one can prevent some common challenges or pitfalls. Getting PEEK injection moulding right pays major dividends. Producing high-quality, defect-free PEEK components allows you to take full advantage of its excellent performance.
To realize PEEK’s benefits, every detail of the injection moulding process must be controlled and optimized. In this article, you will learn the five key factors to consider when moulding PEEK. By following the guidelines from our material you could prevent defects, reduce iterations, and accelerate proficiency with high performance material.
#1 Equipment: Standard Injection Moulding Machines
#1 involves the equipment you use to mould PEEK. PEEK can be moulded on standard injection moulding machines supplied by most of the well-known machine suppliers. Depending on the grade of PEEK that you’ll be moulding, processing temperatures on your injection moulding barrel will be somewhere in the range of 350-400⁰C.
These temperatures can be reached on most standard injection moulders with cylinder heaters without the need for modifications. If modifications are required these are usually for the heater bands or thermocouples/controllers. We suggest you use ceramic heater bands as they provide the most consistent processing. Additionally, consider the use of barrel blankets as they provide heat insulation, with the benefit of energy cost savings.
A general purpose screw is effective. Copper and copper alloys should be avoided (in contact with melt). All metallic components should be smooth and highly polished to prevent hang ups.
#2 The importance of drying PEEK polymer
#2 is all about drying your PEEK polymer. PEEK granules are supplied nominally dry but may absorb moisture from the atmosphere. In our datasheets and injection moulding guide, we provide some guidance on drying. In short, we suggest drying the pellets on trays in circulating ovens for 2–3 hours at 150-160⁰C or, alternatively, overnight drying – please refer to our guidance for further information.
The aim is/should be to reduce the residual moisture content to <0.02%. Dehumidifying or desiccant dryers may also be used and must be capable of maintaining a dew point or saturation temperature of -40⁰C.
#3 Cleanliness is key
#3 is a big requirement – keep it clean! Any contamination should be avoided when processing PEEK. As you will appreciate, most other polymers will degrade at PEEK’s processing temperatures and therefore it is imperative to start with clean drying ovens, hoppers, injection moulders and any other containers used to hold runners or parts. Pull screws and properly clean and brush the barrel and screw before starting to mould PEEK. Check for hang ups in hoppers.
Regrind can be a big source of contamination and we suggest that you use dedicated equipment for the regrinding of PEEK materials. Any contaminants during the injection moulding process will show up as black specs in your final component.
#4 Use the biggest gates possible
Moving along the injection moulding process we come to #4 – PEEK likes big gates. Gate size is dependent on the part volume, number of cavities and component geometry. PEEK is a semi-crystalline polymer and exhibits much higher shrinkage compared to an amorphous thermoplastic.
Moreover, cooling from a much higher processing temperature to ambient causes more shrinkage compared to lower temperature processing polymers. Using the biggest gates possible will enable that you fully pack out your component.
At Victrex, we have a general rule called the 2/3rds rule of the maximum section thickness of your component. Depending on the grade of PEEK that you’ll be moulding this might be a minimum of 1mm for unfilled PEEK and 2mm for compounds. Gate designs such as tab, side or fan gates are most commonly used. Submarine or tunnel gates can be considered for very thin walls or small parts but tend to lead to freeze off during moulding of bigger parts.
#5 Good temperature control
#5 is critical – good temperature control on your mould. As discussed in a previous blog post by John Grasmeder, Chief Scientist at Victrex, on Polymer Crystallinity, the mould temperature is critical to obtain a semi-crystalline component that can fully utilise PEEK’s unique set of properties. Let’s look at some components that are not moulded correctly.
The extremes shown in a simple tensile bar.
Moulded component showing crystalline and amorphous areas.
The brown sections are the amorphous PEEK and the beige coloured sections are semi-crystalline PEEK. To mould PEEK and its compounds successfully one needs to be able to maintain mould temperatures between 170-200⁰C (to avoid quench-cooling into the amorphous state), depending on the grade being moulded. It is important to note that this should not only be the set temperature on the mould, but indeed the surface temperature on the mould. This can be achieved using electrical heaters for smaller parts and oil heaters with isolated flow lines for larger shot sizes or tools with large/deep cores. Consider using insulation boards between the mould and the machine platen as well as packing the tool with thermal insulation for uniform temperature distribution across the mould.
In summary, there are many other factors that play a role in successful PEEK moulding, but the five outlined above, are a good introduction to what is important when starting to mould PEEK.
- Standard moulding equipment can be used to mould PEEK.
- Dry your PEEK pellets well before starting your moulding process.
- Keep the process clean - any contamination may cause problems during the moulding process.
- Use big gates to properly fill your mould and pack out your component.
- Have good control over the mould temperature to ensure semi-crystalline PEEK components.
Victrex´s technical service teams across the globe are available to support customers when injection moulding questions come up. You can also download our Injection Moulding guide and datasheets from our Victrex.com site or contact us through the various channels that are available on our website.
© Victrex plc. 2019. All rights reserved.
Disclaimer
About the author
Carin Burger is a material scientist working at Victrex the past 17 years. She has experience in R&D and technical services. She enjoys her work as part of the EMEA technical service team, working with customers to solve their issues and providing support in design, processing and manufacturing.
About the author
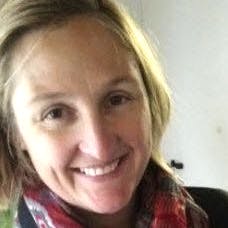