Celebrating Innovation: 5 Amazing Inventions using PEEK Polymer
Everyday design engineers across the world are working on improving or inventing products to make our world better. Whether that’s to improve productivity, profitability, and reputation or to save time, cost, or risk it requires challenging the status quo and looking at new ways of working.
The material choice of each component is a critical decision that determines outcomes for physical components. PEEK, poly-ether-ether-ketone, is one of the world's highest performing thermoplastics. It is a versatile material that can meet multiple engineering requirements at the same time without compromising performance. Thriving in extreme environments, from temperature to chemicals combined with excellent tribological and mechanical performance, making it a popular choice in demanding applications.
In this blog we'll recognise and celebrate the work of some truly remarkable engineers who have pioneered using PEEK in applications, ranging from the rare but crucial, to the commonplace yet important to inspire future innovations.
Have a challenging application that could benefit from PEEK innovation?
The extraordinary inventions you're about to discover didn't happen overnight—they required specialized technical expertise and collaborative engineering support. See how Victrex's innovation capabilities can help solve your toughest design challenges.
100% Total Artificial Heart
The Aeson® total artificial heart is a truly phenomenal feat of engineering brought to reality by the French company Carmat, who's vision is to become the primary alternative to heart transplants with the implementation of their Total Artificial Heart.
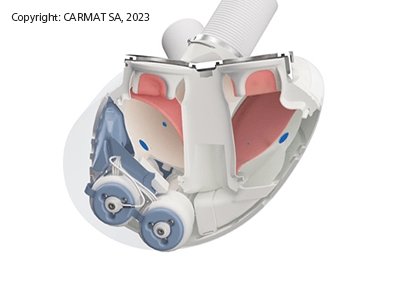
A solution to treat patients suffering with advanced heart failure, their active implantable medical device completely replaces the heart organ with a mechanical pump that mimics the action of a human heart. PEEK is used to create the structural housing of the device because of its biocompatibility and outstanding mechanical properties.
NASA Spacecraft: Out of this world!
High kudos to NASA scientist’s, who invested over six and a half years and spent $1.13 billion on the research and development of the spacecraft and instruments for the successful Juno 2011 mission, the first space mission that flew as close as 2,600 miles to Jupiter’s cloud tops to probe beneath them and answer questions about the evolution of Jupiter and our solar system.

The spacecraft is carrying the Jovian Auroral Distribution Experiment (JADE) instrument that is used to measure electrons and ions that produce Jupiter’s strong aura. JADE contains three PEEK components that were manufactured by Diversified Plastics, Inc. (DPI), which is headquartered in Minneapolis, MN, USA.
The company was selected because of their extensive experience in moulding PEEK. PEEK was proven to have the critical characteristics needed, with sufficient resistance to ultraviolet radiation, a low outgassing profile when exposed to the high vacuum of space, and stiff, strong and lightweight features, as well as complying with “NASA_JSC SP-R-0022A Vacuum Stability’ requirements of polymeric materials for spacecraft applications.
Subsea applications: Smaller, thinner, lighter at scale
Engineers often consider PEEK to create smaller, thinner, lighter critical applications. But what if you want to achieve these things at scale? The great-minds at Magma Global chose PEEK and Carbon fibre to achieve just that, producing simplified subsea architecture – designed to produce up to 6000m / 20,000ft continuous lengths, to operate in challenging subsea environments.
Beyond that, it enables the engineers to innovate subsea architectures for improved efficiency and simplified installation. The added benefit that the carbon-fibre PEEK pipe is 10x lighter in water than the equivalent steel, it simplifies transport and deployment, saving significant time, cost and lowering carbon footprint.
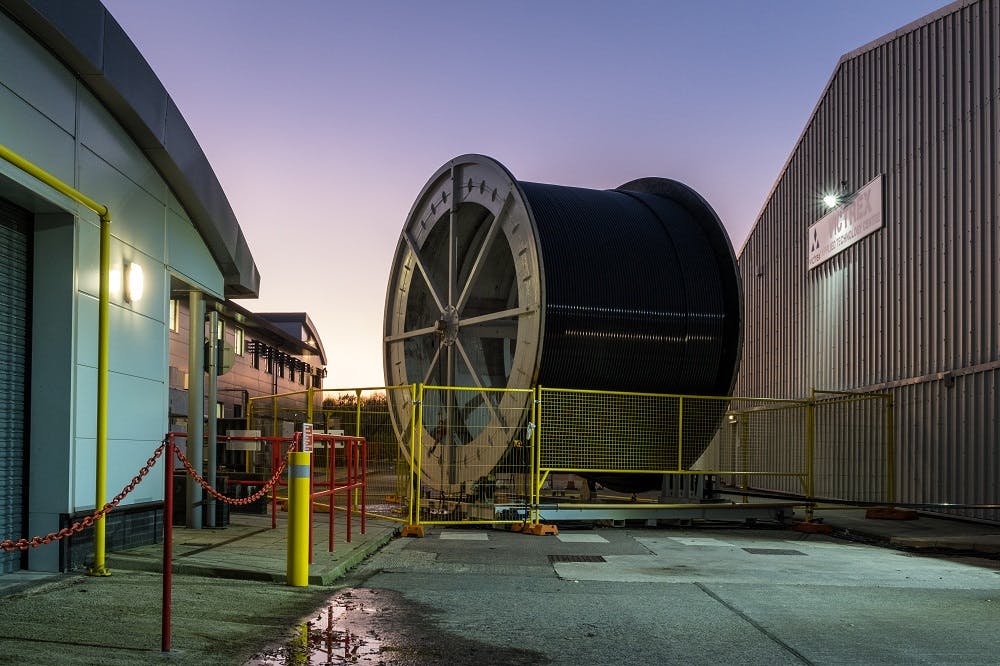
Unlike other materials, as one of the highest performing thermoplastic polymers available, PEEK thrives in these demanding environments, withstanding temperatures up to 200° centigrade (400° F), chemicals, and operational pressures – up to 20ksi (20,000psi), as well as not being subject to corrosion or degradation seen by typical metal materials used.
Revolutionary, strong, faster, lighter impellor
Sometimes it's not the product itself, but a component within a product that makes all the difference and should be celebrated. The Dyson electric motor is a great example of this.
James Dyson described his motors as "Quantum leaps in motor development" producing " faster, more powerful and lighter" motors for home appliances such as floorcare and personal care products. The impellor, a critical, key component for the motor’s performance, is made with PEEK and carbon fibre composite. This material gave the impellor designers the right combination of stiffness and fatigue strength while offering excellent dimensional stability required for precision moulded parts. The result, reimagined precision design that is strong and lightweight that’s needed to realise the performance of above 100,000RPM (revolutions per minute) that help create suction and airflow efficiently.
5. ABS brake systems – innovation that sets the standard
Setting a new standard is clear proof of successful innovation. The anti-lock braking system (ABS) is a critical safety feature that prevents wheels from locking and vehicles from skidding. Estimated to have saved millions of lives, it’s an unsung hero that drivers often take for granted. Governments, however, do not and have made ABS mandatory for passenger cars and motorbikes in Europe and the United States.
Did you know that PEEK is an enabling material in many such systems? Engineering experts select carbon-fibre reinforced PEEK for several functional components of their ABS, realising significant processing and performance advantages.
PEEK parts, which replaced previously used metal, also enabled injection moulding benefits, reducing processing steps and production costs.
Performance wise, this high-performance polymer provides long-term mechanical resistance and abrasion resistance to the brake fluid required by these applications. Plus, the material delivers against multiple requirements for strength and tribological properties. In-situ, the lighter-weight parts reduce the moment of inertia versus incumbent metals, enhancing the overall benefits of system-wide reaction.
Of course, these are only a few examples of how engineers have used PEEK to innovate. If PEEK has been pivotal for your design goals, I’d love to hear about it, get in touch and share your story!
Related Victrex Content
- Lighter, Faster, Greener: The Pursuit for the Shape of Aerospace’s Future
- Making the Change to Safe Alternatives for a Safer Planet: The PFAS Challenge
- Unleashing the Power: Enhancing e-Bike Performance with High-Performance PEEK Polymer Gears
About the author
Melanie Embery is Head of Marketing Communications, Globally at Victrex. She has over 20 years marketing experience in software, manufacturing and marketing sectors and held several marketing positions at Victrex. Melanie holds an MSc Masters Degree in Professional Practice with a focus on Innovation Leadership and Change Management from Lancaster University. (LinkedIn Profile)
About the author
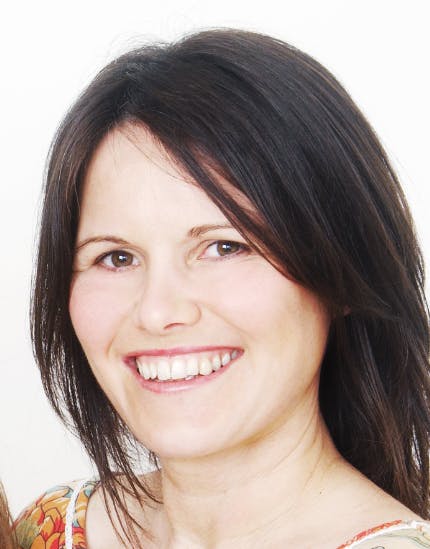