Industry 4.0 (part 2): The material performance challenge
This article was originally published on September 3, 2018, and has been edited on August 31, 2023.
Organisations recognise the importance to propel manufacturing operations using the digitisation benefits of Industry 4.0, as shown in a global survey that 68% of respondents regarded Industry 4.0 as a top priority and 70% said their companies were already piloting or deploying new technology. 1
In part 1 on Industry 4.0 we raised a crucial question: With the focus of Industry 4.0 typically on artificial intelligence (AI) and software for automation and data exchange, is the challenge of whether the hardware can keep up with the pace often neglected? A couple of examples show that it can be worth to dig deeper.
Micro requirements to achieve the targets on the macro level
Materials used for components in sealing applications are a case in point, because they can function as critical factors for success. Commonly there are two key needs that trigger material selection:
- The requirement for greater efficiencies (regarding manufacturing and assembly, operational, and overall cost reduction)
- Improving performance (meeting reliability targets and reducing downtime)
A material that can contribute to meet these needs is VICTREX™ PEEK, a high-performing polymer, already being adopted, for example in industrial, oil and gas and automotive sectors. Used in many applications within harsh and demanding environments, it is proving its capability to push boundaries further. The reason: PEEK can support multiple requirements, whilst alternative materials often can only meet specific single needs. For example this light weight, high strength polymer is extremely durable, providing high resistance to wear, operates in extreme temperatures and is also chemically resistant, with purity essential for critical applications within the food and beverage industry.
Sealed to survive the extremes
Effective and efficient sealing is an essential part of almost every modern industrial process where gases, liquids and solids are being transported. Seals are needed wherever the containment of these commodities is completed (such as end-caps), measured (flowmeters), controlled (valves) or separated from moving parts. The broad range of application possibilities requires an equally diverse range of sealing technologies and products. One example is split-ring seals made with PEEK which are often used for reciprocating motion, and in hydraulic swivel joints and transmissions. They have proved extremely reliable due to the polymer’s inherent toughness and flexibility enabling the split-ring seal to be installed without breakage, whilst high strength and creep resistance provide a long service life under aggressive conditions.2
Ball valve seats for controlling a range of aggressive fluids and gases are another application for the high-performance polymer. This versatile material can provide an excellent seal with the steel ball, plus high resistance to steam means that it is also used in control valves in steam systems to provide durable, effective seals, enabling tight shut off and long life – thereby reducing leaks and costly downtime and maintenance.2
Many of these material attributes carry over into the use of PEEK in the food manufacturing industry, with the advantage that many relevant polymer grades are compliant with EU, FDA, NSF, 3A, WRAS regulations 3 . Stainless steel, for example, has typically been used for chains requiring high heat resistance. However, in food processing conveyor belt chain applications, high heat resistance and chemical resistance are essential requirements. Chains made with VICTREX™ PEEK polymer and its compounds can withstand exposure to temperatures as high as 260°C (500°F) and offer notable long- term resistance against detergents such as hydrogen peroxide and caustic soda.
Growth advantage accessed through both soft- and hardware
Companies are already planning advanced levels of digitisation to achieve lower costs and increased efficiency as part of pursuing their Industry 4.0 strategy. Software and AI are key to automation. However, there are also opportunities through hardware and material selection, in working with material experts to understand how high-performing polymers can be used to solve specific needs to keep automated environments moving. For several decades, VICTREX™ PEEK has been used across industries in numerous applications and demonstrated its high performance capability to meet Industry 4.0’s hardware needs.
References
1) McKinsey & Company, What are Industry 4.0, the Fourth Industrial Revolution, and 4IR? (2022) https://www.mckinsey.com/
2) Small, Geoff: Sealing Technology, 2014, issn 1350-4789
3) Customers must naturally check for themselves that the PEEK they actually select is compliant with these regulations
About the author
Steve Dougherty is Director Manufacturing & Engineering at Victrex. He joined Victrex in October 2011 as an experienced industrial marketer and strategist with extensive global marketing experience in B2B markets. Prior to joining Victrex, Steve held positions in operations and marketing at Cabot Corporation, Ineos & ICI. Steve holds a BEng degree in Chemical Engineering from the University of Surrey, England, and an MBA from Manchester Business School.
About the author
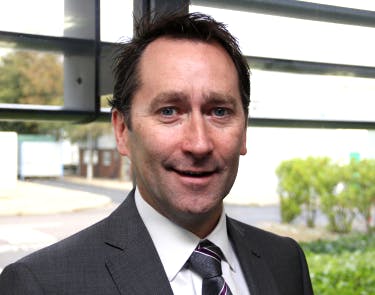