Managing the fast-accelerating food requirements of a growing planet
9.7 billion
The world’s population is growing fast, with the UN’s latest figures showing an estimated population of 9.7 billion by 20501, an increase of ~ 60% since 2000.
With new challenging trends that include the rise of convenience and health-food snacks, as well as more mouths to feed globally, increased demand is being placed on the food processing and handling (FP&H) industry.
The key to coping with this growth is understanding the new and different types of demand from consumers. For example, we now hear calls for beverage machines that allow users to create and customise the flavour of their drinks. Then there is the impact of changing demographics, such as rising demand for healthy food on-the-go, with 63% of millennials replacing meals with snacks because of busy lifestyles2. Add to that China’s working age population, due to grow 20% by 20203, and there will inevitably be an increased demand for specialized on-the-go food.
Emerging markets are leading the way, with 35% of the US$100 billion FP&H equipment market originating in Asia—expected to account for 50% of growth in the sector by 20214.
Are we on the brink of a global food shortage crisis?
The first need to address is that of producing significantly more food, at scale and speed, and safely, for a changing demographic, without adding to the 1.3 billion tonnes of food that is lost or wasted globally each year5.
There are of course different regional regulations to consider, as well as the implications these have on the processes, equipment and chemicals used on the production line. While MERCOSUR, the South America trading bloc, recognises FDA or EU10/2011 approval, this is not the case for both China and Japan, which are both migrating to independent approval systems.
Then there is the increased demand for meat and health foods coming from the growing middle-class population. A 2015 Grantham Mayo van Otterloo report stated that the middle class are eating more meat than ever before, while also putting a strain on soy and grain reserves. The report also stated that the prices of wheat, corn, soybeans, and rice were twice what they were in 2000, with prices expected to double again in the next couple of decades6. To counter this, the FP&H industry must look for ways to keep costs down, from processing methods to packaging.
If we don’t achieve the flexibility to meet the various regional regulations, or maintain the strength in the supply chain to meet the growing demands for meat, soy, rice and more, then that global food shortage crisis may not be as far away as it first seemed.
Measures to help take more control
To help reduce waste requires an even bigger focus on quality and hygiene on the production line. The adoption of regulatory compliant materials such as the recently introduced VICTREX FG™ polymers7 for food manufacturing equipment and components can result in lower maintenance, reduced contaminants and less risk of product recalls. This is because they are resilient to stringent industrial cleaning processes, harsh chemicals, and powerful processing methods, without suffering degradation.
Non-thermal food processing methods continue to help extend shelf-life by inhibiting or killing microorganisms, with minimal impact on the nutrition and quality of the food; these technologies are estimated to grow at CAGR 8.4% to US$1.22 billion by 20228. Methods include ultra-high-pressure processing (HPP) techniques, ionizing radiation, ultrasound, pulsed light and pulsed electric fields to name a few. Based on a 2017 survey in the US, the most frequently adopted non-thermal processing technique was HPP, with a 36% share9.
Other more rapid food-safety techniques are also being developed, with microbiological testing and new biosensor technology to identify pathogens in food samples more quickly and accurately; fast and efficient transcriptomics, proteomics and biosensor-based solutions aim to help improve screening for chemical contaminants10.
For manufacturing equipment, technologies such as Internet of Things (IoT) are helping to reduce the risk of food illness epidemics and further food waste from recalls, with sensors that monitor production state, shipping time, and temperature.
Supply chain security and control measures
The security of supply of production line materials and components is key to meeting manufacturing demand. Materials from suppliers that have reliable stock allows access to the required components to expand or update parts in the production line, exactly when they are needed.
Developing equipment that is compatible with areas of automation and connectivity now undergoing growth through the formation of the IoT is necessary to enhance productivity and future-proof equipment. Robotics and the automation of equipment are increasingly prominent, beyond packaging operations where they are already prevalent, to aid lean manufacturing and to maximise efficiencies. Based on a Grant Thornton survey, 89% of UK Food and Drink Manufacturing companies are involved in new product development, and 73% are innovating in manufacturing process automation11.
Smarter equipment is becoming available, at lower cost, capable of performing self-diagnosis and preventative maintenance cycles, which then reduce the risk of failure and downtime. In addition, increasingly sophisticated inspection equipment now delivers faster read times and throughput, while capable of detecting contamination at even higher resolutions. These developments place additional demands on the materials used in the manufacture of the equipment.
While you can’t always control crop yields or consumer wastage, the food processing and handling industry can certainly take control of technology, materials, processing and production line quality.
As the food and beverage industry enters a new era, creating a sustainable supply chain that can adapt with changing demands and new trends will keep a growing population fed, efficiently and sustainably, while taking care of the planet.
Interested in learning more about the next-generation of high performing PEEK polymers for food contact? Drop me an e-mail or visit victrex.com.
- UN report: https://population.un.org/wpp/Publications/Files/WPP2019_Highlights.pdf
- Innova Market Insights, 2019: (https://www.nutritioninsight.com/Webinars/top-ten-trends-2019.html)
- United States Census Bureau: Census.gov
- McKinsey on Food processing and handling Ripe for Disruption report: https://www.mckinsey.com/~/media/mckinsey/industries/advanced%20electronics/our%20insights/whats%20ahead%20for%20food%20processing%20and%20handling/mckinsey-on-food-processing-and-handling-ripe-for-disruption.ashx?auto=compress,format.
- Food & Agriculture Organization of the United Nations: Do good save food! Nine easy tips to reduce food waste: https://www.fao.org/3/a-c0084e.pdf
- Business Insider, 2015: https://www.businessinsider.com/growing-middle-class-is-straining-food-resources-2015-8
- Victrex: https://www.victrex.com/en/food
- Markets and Markets Market Report, 2018: https://www.marketsandmarkets.com/Market-Reports/food-non-thermal-processing-market-158213636.html
- Harlin Kaur Saroya, Masters Thesis: https://pdfs.semanticscholar.org/de57/b2b51bec69fac3e5cc1e0d3f660e345f444d.pdf
- Steinfeld, H., et al. (2006) Livestock’s long shadow - Environmental issues and options. The Livestock, Environment & Development Initiative. FAO/World Bank/EU/IFAD Sponsored Report
- Food and drink federation: The Food & Drink Federation (fdf.org.uk)
© Victrex plc. 2019. All rights reserved.
Disclaimer
About the author
Alice Marsden is a Strategic Marketing Manager at Victrex for the Manufacturing and Engineering business unit. She joined the company in 2012, holding roles within R&D before joining the Marketing function in 2017. Alice holds an MRes in Materials Engineering and is a qualified Project Manager (PMQ).
About the author
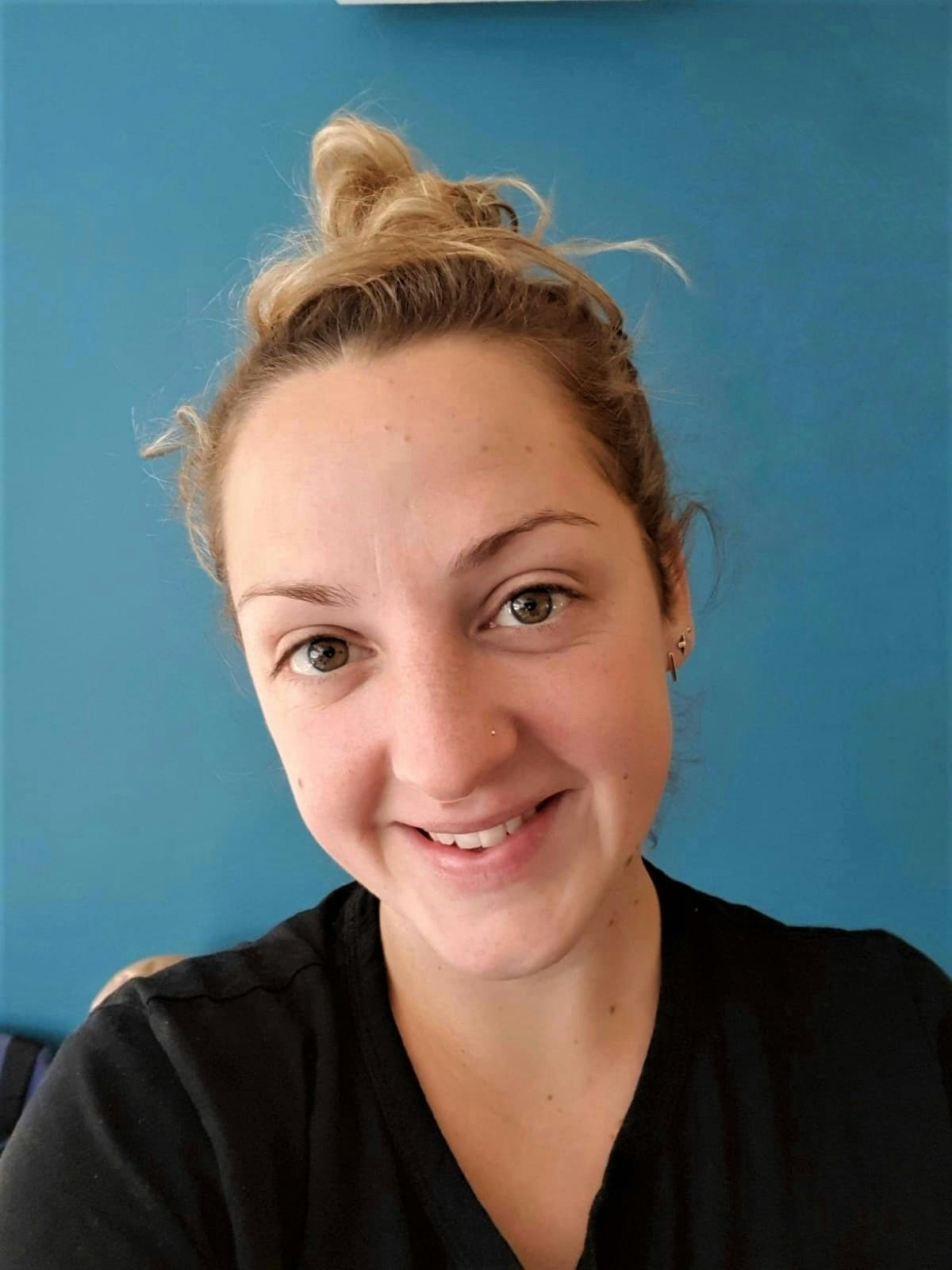