The EU pushes sweeping improvements in vacuum- cleaner design
In September 2017, new EU eco-design rules that ban the sale of noisy and inefficient vacuum cleaners came into effect. The rules reduce the maximum power rating from 1,600 W to 900 W and limit the maximum noise level to 80dB. Vacuum cleaners are also required to pass two durability tests - one for the main hose that sucks up the dirt and another for the motor, and at the same time bust the myth for consumers – higher power equates to better performance!
Despite the controversy, the new European legislation, designed to boost energy efficiency and reduce carbon dioxide emissions, is expected to help consumers save money on electricity bills and vacuum cleaners since machines with better durability will need to be replaced less frequently.
Energy-efficient motors without compromise
Manufacturers, however, are on the carpet. Complying with the new regulations won’t be easy. Major challenges lie ahead. How do you make a motor more energy-efficient without compromising performance? It’s all well and good cutting power consumption, but can reducing motor power mean greater performance efficiency when it comes to the actual job – sucking up dirt and dust? Clearly, companies inside and outside the EU will have to come clean about this: only sweeping innovation in design and construction materials will supply the answers.
Clever use of material design and the trend of replacing metal with high-performance polymers could be the answer. One of the highest performing thermoplastics is VICTREX™ PEEK polymer. It has long been recognised for its outstanding mechanical properties and performance, having in particular a strength-to-weight ratio equal to or in some cases better than that of metals. Designers immediately have more options with this easy to process, advanced thermoplastic polymer, fewer materials constraints, and greater design freedom. Indeed the use of VICTREX™ PEEK polymer can also when replacing metals reduce part cost, and enable rapid scale up of production. Little wonder that we have seen our material replacing metals in gears for automotive, in brackets for aerospace, in motors and fans replacing Aluminium, and reinforced PEEK replacing metal in the construction of subsea piping for Oil and Gas operations.
Talk to our expert about designing the next generation vacuum cleaner
Create a buzz, not noise
Take vital components such as an impeller. If key parts are made from light-weight VICTREX PEEK rather than metal, energy efficiency can be improved by up to 2 %. Moreover, performance and durability can be enhanced enabled by high speed operation (or rotation) – including at speeds in excess of 100,000 rpm – with minimum deformation, while noise can be reduced by up to 50%. In addition, the high-performing polymer is resistant to a wide range of household chemicals, heat and moisture – and can enable part cost and weight reductions – and enable rapid scale up of new designs.
Designing for the future
After all, addressing the challenges and changes demanded by the EU, and quite possibly by consumers in many other regions, could be easier than manufacturers of vacuum cleaner might have thought. The future of designing powerful smaller motors with durable materials solutions has already begun – but not only for the sake of complying with regulations.
Greater energy efficiency, including less electricity consumption or the potential to extend battery life, contributes to a green(er) future. At Victrex, we fully support sustainability targets as well as manufacturers as they ramp production and achieve both economies of scale and a faster time-to-market.
© Victrex plc. 2018. All rights reserved.
Disclaimer
About the author
Paul Corscadden, Head of Technology, Victrex
After graduating from Nottingham University in Materials Science and Engineering, Paul obtained a PhD at Liverpool University on the subject of “Flow of Reinforced Thermoplastics in the Injection Moulding process”. In his 30 years industrial experience he held a number of operational and research positions in Automotive, Aerospace and Electronics. Paul has been with Victrex for 6 years and is head of R&D for Electronics business unit.
About the author
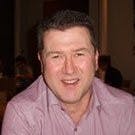